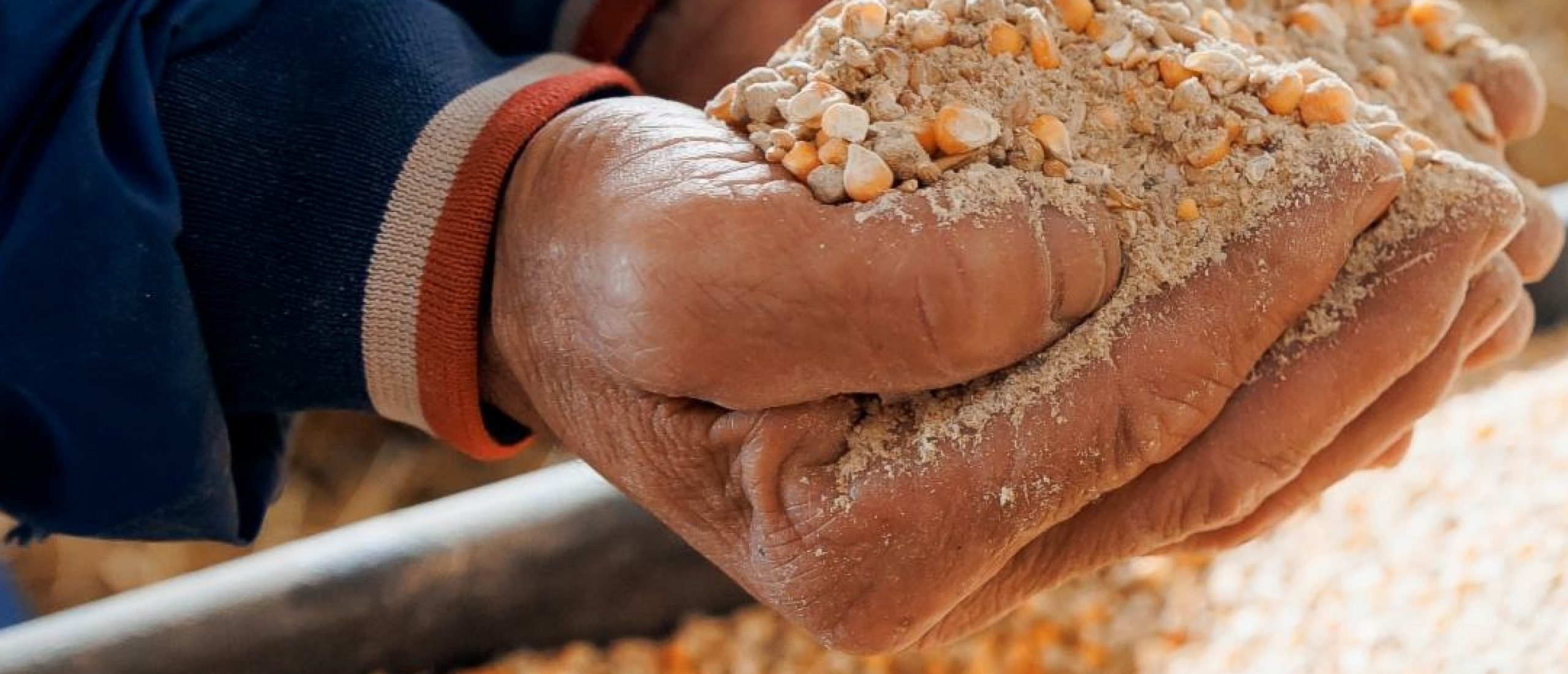
DSM Twilmij optimizes business processes with SAP in public cloud
SAP S/4HANA Public Cloud Edition streamlines production and provides valuable insights
How do you produce and deliver seasonal and highly customized premixes for animal feed on a large scale and within strict deadlines?
DSM Twilmij, DSM's site in Stroe, found the answer in standardization on SAP S/4HANA Public Cloud Edition. SAP partner Scheer guided the process. DSM Twilmij has been part of DSM-Firmenich, DSM's food technology division, since 2017. This location produces and supplies premixes for animal feed to compound feed companies. The premixes contain a sophisticated mix of vitamins and other additives that play an important role in the health of livestock.
Complex puzzle
The production and delivery of the premixes is a complex puzzle. The premixes consist of some 20 to as many as 60 different raw materials. The exact composition not only changes per season, but is also tailored to the customer. For example, cows that are primarily housed in the barn receive a different mix than cows that primarily graze in pastures.
Despite the complicated customization process, DSM aims for a delivery time of no more than five days. This allows compound feed companies to keep their inventories low and thus their required operational costs and storage capacity. In this way, the company is an important strategic partner for the compound feed industry.
Functional requirements
Making this complex production and delivery process manageable requires a robust IT environment. One that not only streamlines the end-to-end processes, but also simplifies the complicated costing. "Moreover, the new system had to fit well with the DSM-wide SAP environment," said Christian Veldkamp, Manager Control Animal Nutrition & Health at DSM-Firmenich. "The old custom system did not yet meet DSM standards."
In addition, the new environment had to be able to integrate with SAP Central Finance. "In fact, in parallel with this implementation, DSM made the switch to this central finance environment. Ultimately, the various public cloud environments within DSM had to be able to talk to it," Veldkamp clarified. "In doing so, this implementation served as a kind of template for other premix locations of DSM."
Integration with production environment
Fit-to-standard was therefore the starting point. In doing so, DSM opted for standardization in the public cloud, with SAP S/4HANA Public Cloud Edition as the brains of the new IT environment. Production orders from SAP S/4HANA go to the MES systems (Manufacturing Execution Systems), which control physical production. In this, the SAP BTP acts as the network and provides real-time communication between these environments. BTP is also the platform on which customization and additional applications run.
The real-time link between SAP and the MES environment offers many advantages. For example, the MES environment sends information about the production process back to SAP, such as the ingredients used. As a result, DSM always has insight into the cost price and current inventory status, based on actual production activities. The company can also react quickly to changes and use analyses to detect where things could be even more efficient.
Best practices
During implementation, the parties strived not only for a robust and standardized IT environment, but also for precise alignment with industry best practices. "Thanks to that approach, we stayed very close to those best practices. This is how we ensured the reliability and future-proofing of the system," Veldkamp says.
Despite the focus on best practices and standardization, the unique needs of DSM Twilmij were kept in mind. "In some cases where specific requirements could not be fully addressed within the standard SAP S/4HANA environment, we opted for a flexible solution. An event-based side-by-side extension was developed on the SAP Business Technology Platform (BTP). This allowed us to keep the core of the system 'clean' while still meeting the need for real-time data and processes."
Crucial change management
Moving from a custom system to a standardized SAP environment not only had a major impact on the IT infrastructure, according to Ferry Bogaards, Managing Partner at Scheer. "Change management was crucial to the success of this project. Through iterative workshops, we continuously collected feedback from employees."
However, the full impact of the change only became clear during user acceptance testing. "We even postponed going live once, in order to better prepare employees for the new ways of working. Ultimately, the success of an implementation like this hinges on their acceptance."
New functionalities
The new environment went live in 2022, but that was not the end of the project. "Actually, a project like this is always 'evolving.' We regularly add new functionalities through applications on the BTP. By doing so, we easily change along with business requirements while keeping the standardized 'core' as clean as possible. With that setup, DSM is ready for the future."
The Podcast
Link to the OpenSAP Podcast from DSM Twilmij - Dutch Language only