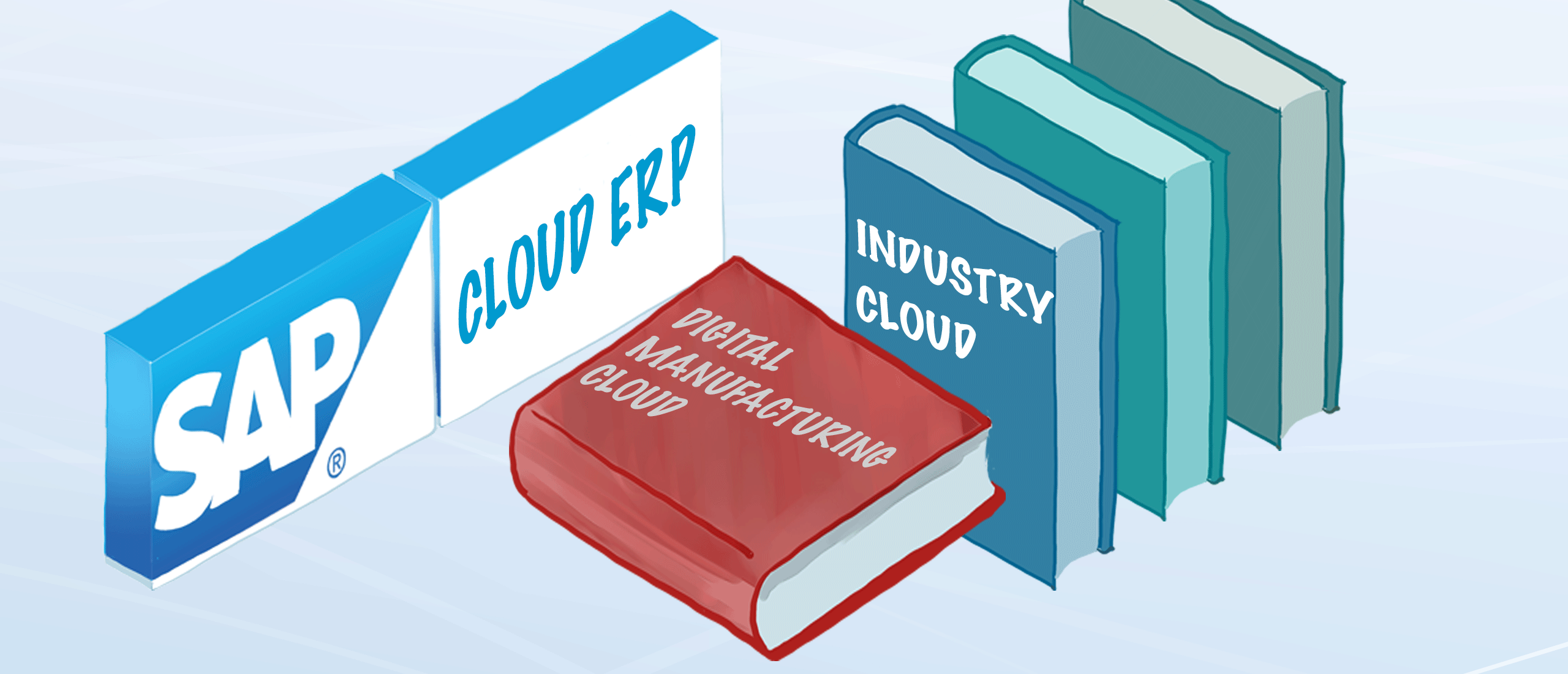
Digital Manufacturing - Execution
The SAP Digital Manufacturing Execution is to orchestrate and control your shop floor. The SAP Digital Manufacturing Execution solution is designed to enhance manufacturing efficiency and optimize processes. This Execution Platform integrates real-time monitoring, customizable dashboards, and advanced resource management to streamline manufacturing operations.
Key Capabilities
- Monitor the entire manufacturing process to optimize resources and execution
- Role-specific Fiori and operator dashboards
- Fully configurable Production Operator Dashboard (POD) that supports drag & drop and preview
- Monitor OEE and manage downtime events
- Resource Orchestration to manage shop floor workflow and labor assignments
- Automation interfaces to provide for shop-floor-driven manufacturing events and data collection
Digital Manufacturing Execution Tasks
SAP Digital Manufacturing Cloud for Execution: Work in process management and reporting:
- Manage and release orders for execution on the shop floor
- Production operators use the configurable PODs (Production Operator Dashboards) that were created in the POD Designer to capture and report execution data
- An SFC is a unique WIP identifier representing a specific instance of the material being built during the manufacturing process and allows for full traceability of the product.
- The SFC represents the quantity of the product to be produced, depending on the lot size of its material. An SFC can be a serialized or non-serialized (lot).
Execution and Discrete Manufacturing
The Production Operator Dashboard (POD) in SAP Digital Manufacturing is a customizable and interactive interface designed for manufacturing operators. It provides real-time visibility and control over production processes, allowing operators to monitor key performance indicators, manage tasks, and quickly respond to manufacturing events. The POD's user-friendly design, including drag-and-drop functionality and preview options, enhances operational efficiency and decision-making on the shop floor.
- Support operators with a highly flexible and intuitive user interface (POD)
- Configure and design the POD based on user requirements
- Display execution-relevant information on production orders
- Guide operators through work instructions in the POD
- Support of data collections
- Logging of defects and subsequent rework and repair actions using the nonconformance functionality
- Provides product serialization and re-identification
- Recording of assembled components for traceability and to trigger goods movements
- Monitor OEE using established KPIs in the POD
- Post-operation activity-level yield confirmations happen automatically, as well as goods receipts as units are completed
Execute Production Order in Order POD
Operator can see the details of the order (including batch) and execute the following activities:
- Start Operation
- Report Activities
- Report Yield and Scrap
- Report Material Consumption
- Data Collection
- Complete Operation
- Report Goods receipt header material
- Report Goods Receipt for Co-products and Batch products
- Valuate batch during Goods receipt (update batch characteristics)
The operator can execute the following activities in Post-Production POD:
- Report Goods receipt for Production Order
- Report Data Collection for Production Order
Overall Equipment Effectiveness
- Optimizing the machine efficiency by utilizing the Overall Equipment Effectiveness (OEE) functionality
- Real-time visibility via related KPIs
- Production Operator Dashboard (POD) is configured to show OEE KPIs.
- The straightforward user interface allows production operators to report machine status change easily
- Detailed OEE insights and root cause analysis
Work in process management and reporting
Capture the digital twin of the production process presented by the following reports:
- The Product Genealogy Report displays the details of the component data collected for an SFC
- The Product History Report displays the activity of an SFC over a period of time for Discrete Industries and a Batch over a period of time for Process Industries (see more details)
Execution and Process Industries
Designed specifically for the process industry, it enables businesses to optimize production processes, ensure quality and compliance, and enhance operational agility. By leveraging real-time data and analytics, SAP Digital Manufacturing Execution empowers companies to make informed decisions, reduce downtime, and maximize productivity.
Capabilities for Consumer and Process Industries
- Extend Master Recipes integrated from S/4HANA with Work Instructions, Data Collections and Process Parameters;
- Execute and Split Batch related Process Orders in the Production Order Dashboard (POD)
- Create and Valuate Batches for Main Products as well as for Co-Products and By-Products during Production and search and Consume batches based on characteristics
- Confirm process order phases with Yield, Scrap, and Activities integrated with S/4HANA
- Post and Cancel goods movements for goods issues and receipts seamlessly integrated with S/4HANA
- Record inspection results with Inspection Points integrated with S/4HANA QM
- Integrate with the Shop Floor in a bi-directional way using Equipment Connectivity (Production Process Designer*)) and Plant Connectivity (PCo)
- Enable Post-Production Reporting
- Customize your application with the POD Designer
- Print customized Labels
- View product history report for produced batches
Process Industry – “Manage Recipe” App
- Integrate Master Recipes with S/4HANA
- Maintain execution of relevant data such as Work Instructions or Data Collection parameters in DMC
- Graphical interface for recipe display
- Integrate Production Versions with S/4HANA Cloud
Process Industry - Production Operator Dashboard (POD)
- Integrate process orders with S/4HANA
- Provision of the new Order POD to support order and batch-based execution of process orders with batches
- Guide Operators with a highly flexible and intuitive user interface (POD)
- Configure and design the POD based on user requirements
- Support of Data Collection to collect execution-related data
- Record inspection results for process order operation/phase (inspection lot type 03) and integrate with S/4HANA
- Log Defects for an Order, which can be viewed in the Product History Report
- Report downtimes from POD to calculate OEE availability
Product History Report for Process Industry
- The existing PHR report has been enhanced to enable use by Process Industry Customers.
- Input parameters and report terminology will be set automatically either to Process or Discrete based on the Industry type for the Plant specified in a User profile.
- Users can search by Batch, Material, or Order after pressing a value help button.
Modular Production
Modular production in SAP Digital Manufacturing refers to the flexible and scalable approach to manufacturing processes, where production systems are designed in self-contained, interchangeable modules. This concept allows manufacturers to quickly adapt to changing production requirements, market demands, or new product introductions. By integrating with SAP's digital tools, modular production enhances efficiency and agility, enabling manufacturers to reconfigure production lines and processes with minimal downtime and optimal resource utilization. This approach is particularly valuable in industries requiring high customization and rapid response to market trends.
Innovation Highlights
- Dynamic Routing: Enable modeling of flexible routings and Take Dynamic Production Dispatching on an optimal routing path
- WIP Transport: Integrate WIP logistics to warehousing logistics and Enable tracking of WIP between production operations
- Supply to Cell: Enable dynamic staging of components and Reduce stock-based restrictions
- Visualization: Provide real-time insights on production, logistics, quality, and maintenance
- Analytics: Identify resource bottlenecks and Analyze and improve past decisions