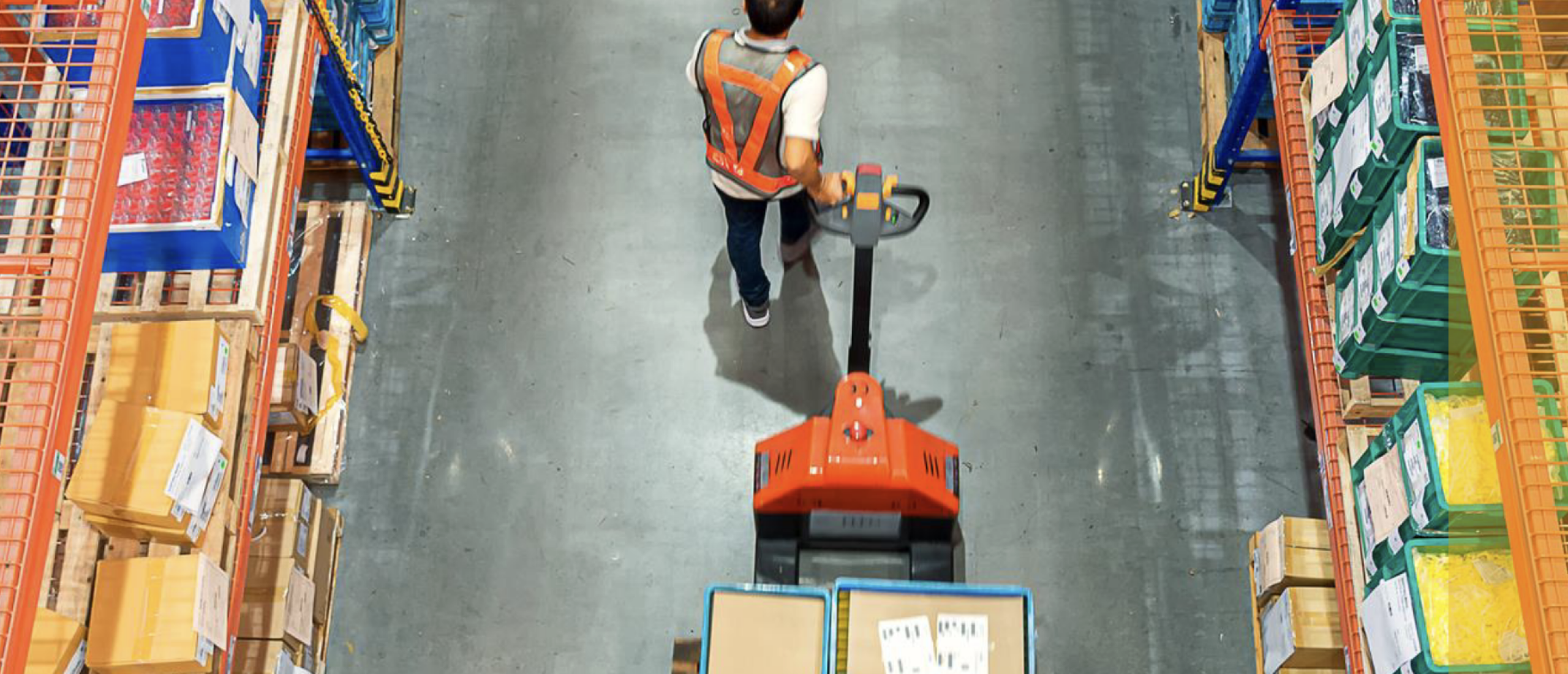
In the picture: Warehouse Management within SAP S/4HANA Cloud, Public Edition
Warehouse Management SAP S/4HANA Cloud, Public Edition
In this Blog, I want to share the capabilities of warehouse management as part of the functionality of SAP S/4HANA Cloud, Public Edition. The reason of paying attention to warehouse management is the lack of awareness of the true capabilities of the Warehouse Management features within SAP S/4HANA Cloud, Public Edition.
In this blog you will find an overview of the warehouse management features we have implemented recently, details about integrations and the cross-topics. Finally an overview of the existing functionality of warehouse management of the 2308 release of SAP S/4HANA Cloud, Public Edition.
SAP History with Warehouse Management: SAP WM and SAP EWM
SAP plays a long lasting role in the support of warehouse management. In the area of SAP ECC there was the SAP Warehouse Management (WM) and the SAP Extended Warehouse Management (EWM) solutions. SAP WM and SAP EWM are both used to define the new Warehouse Management features within SAP S/4HANA Cloud, Public Edition. This is not a 1 to 1 copy and paste action, as the concepts of warehouse management and the integrations with other business areas (like Production, Asset Management, Transportation) within SAP S/4HANA Cloud, Public Edition are different and evolved based on current market demands.
The Warehouse Management functionality within SAP S/4HANA Cloud, Public Edition is perfect to support most production-, service- and wholesale companies.
Scheer's experiences with Warehouse Management
The table below contains an overview of the Warehouse Management Features - in alphabetical order - and the indication of usages. All reference cases are production companies with single to multi locations across different countries.
Project Backgrounds:
A: Manufacturing, integrated with Warehouse Management
B: Manufacturing, integrated with Warehouse Management, usages of Zetes barcode scanners
C: Manufacturing, usages of embedded barcode scanners
D: Consumer Products, usage of embedded barcode scanners
Usages of Functionality
Warehouse Management Features | Project A | Project B | Project C | Project D |
ABC Analyses |
|
|
|
|
Batch Management | x | x | x | x |
BIN Management | x | x | x | x |
Cross Docking Preallocated Stocks |
|
|
|
|
Customer Returns |
| x | x | x |
HU Management | x |
| x | x |
Layout Oriented Storage Control | x |
|
|
|
Barcode Reader Embedded |
|
| x |
|
Barcode Reader API (like Zetes) |
| x |
| x |
Physical Inventory | x | x | x | x |
Put Away Strategy | x | x | x | x |
Quality Management | x | x | x | x |
Replenishment |
|
| x | x |
SAP Warehouse Operator App |
|
|
|
|
Serial number Support | x |
|
|
|
Stock Consolidation | x | x | x | x |
Stock Removal Strategy | x | x | x | x |
Wave Management |
|
|
|
|
Integrations and Cross Topics
Warehouse Management | Project A | Project B | Project C | Project D |
INTEGRATIONS |
|
|
|
|
Transportation Management |
|
|
|
|
Productions | x | x |
|
|
Material Flow System (API) |
|
|
|
|
Plant Maintenance |
|
|
|
|
CROSS TOPICS |
|
|
|
|
SAP Fiori Interface | x | x | x | x |
Best Practices | x | x | x | x |
Monitoring & Analytics | x | x | x | x |
In-Apps BAdIs, Custom Fields |
|
| x |
|
Side-by-Side Extensions |
|
| x |
|
Synchronous Goods Movements | x |
|
|
|
Edit Distributed Deliveries |
|
|
|
|
Warehouse Management Features
Below an overview of the features of warehouse management, in alphabetic order.
ABC Analysis:
ABC analysis is a technique used in inventory management to categorize items based on their importance. The ABC analyses helps organizations to prioritize their inventory management efforts based on the value and demand of items.
Batch Management:
Batch management involves tracking and managing groups of items produced or received together. This is crucial for industries where items from a single production batch or lot must be stored and managed as a unit to ensure traceability and quality control.
BIN Management:
BIN management refers to the process of defining and managing storage bins within a warehouse. Storage bins are physical locations where goods are stored. BIN management involves categorizing bins based on their attributes, such as size, capacity, and location within the warehouse. These bins are then used for organizing inventory and optimizing storage space.
Cross Docking with Pre-allocated Stocks:
Cross docking involves directly transferring incoming goods from the receiving area to the outbound shipping area without intermediate storage. The cross docking with preallocated stocks feature ensures that items are assigned to orders and automatically directed to the shipping area for faster fulfillment.
Customer Returns:
SAP S/4HANA Cloud, Public Edition handles customer returns by allowing organizations to process returned goods efficiently. The returned items are put away in appropriate storage locations and can be inspected for quality before reintegrating them into inventory.
HU Management (Handling Unit Management):
Handling Unit Management involves grouping materials together into handling units, such as pallets, boxes, or crates. This simplifies the handling and tracking of goods during warehouse processes like goods receipt, putaway, and shipping. Handling units can contain multiple items , so called mixed or nested Handling units and are assigned unique identification numbers.
Layout Oriented Storage Control:
This feature involves configuring the warehouse layout to influence storage and retrieval processes. It takes into account factors like storage bin distances, storage capacities, and material characteristics to define how goods are stored and picked.
Process Oriented Storage Control is at this moment not available but will be in one of the 2024 releases.
Barcode Scanners with RF (Radio Frequency):
This feature enables warehouse operators to perform tasks using handheld RF barcode scanner devices. Operators can receive, put away, pick, and perform other warehouse activities using wireless communication with the SAP S/4HANA, improving accuracy and efficiency.
This is the so-called embedded possibility to scan, but there is also the possibility to use APIs for connecting to external barcode scanning applications such as Zetes.
Physical Inventory:
Physical inventory is the process of verifying the actual inventory levels in the warehouse against the recorded inventory levels and provides tools to plan, execute, and manage physical inventory counts accurately, helping to identify discrepancies and maintain accurate inventory records.
Putaway Strategy:
The putaway strategy defines how incoming goods are assigned to storage bins within the warehouse. Different strategies can be employed based on factors like item characteristics, storage availability, and proximity to picking areas. These strategies ensure that items are stored in the most optimal locations for efficient retrieval during order picking.
Quality Management:
The quality management functionality within SAP S/4HANA Cloud, Public Edition allows organizations to define and enforce quality control processes for inbound, outbound and production. It ensures that items meet specified quality standards before they are moved to their designated storage locations or shipped to customers.
Replenishment:
Replenishment refers to the process of moving goods from bulk storage areas to picking areas to ensure that sufficient stock is available for order fulfillment. SAP S/4HANA Cloud, Public Edition supports automatic or manual replenishment strategies to maintain optimal inventory levels for efficient operations.
Serial Number Support:
SAP S/4HANA Cloud, Public Edition supports the tracking of individual items using serial numbers. This is important for industries that require unique identification and traceability for each item, such as electronics or high-value products.
Stock Consolidation:
Stock consolidation involves combining multiple smaller quantities of the same item from various storage bins into a single storage bin. This optimizes storage space and makes it easier to manage and retrieve inventory.
Stock Removal Strategy:
Stock removal strategy determines the sequence in which items are picked from storage bins for order fulfillment. Strategies are designed to optimize the picking process by considering factors such as item demand, item storage location, and order priorities.
Warehouse Operator App:
The SAP Warehouse Operator app is a mobile application that provides a user-friendly interface for warehouse operators to perform tasks using smartphones or tablets. It simplifies day-to-day warehouse operations.
Wave Management:
Wave management is the process of grouping and sequencing warehouse tasks, such as picking and packing, to optimize efficiency. Wave management functionality ensures that orders are processed organized, reducing travel time and improving order throughput.
With wave management you can combine outbound delivery order items into waves to then create picking warehouse tasks across all items by releasing the wave.
Integrations WM
Two levels of integrations
- Embedded with other SAP S/4HANA Cloud, Public Edition functionality.
- API integrations with other SAP or Non-SAP solutions
Transportation Management (TM) Outbounds:
Integration with Transportation Management (TM) ensures a smooth flow of goods from the warehouse to the transportation network. Key integration points include:
- Sales Order creation
- Freight unit created automatically based on the sales order.
- Freight order created which manages transportation planning, carrier selection, and route optimization. This integration ensures that the suitable carrier is chosen and the optimal route is selected.
- Creation of the outbound delivery based on the freight order.
- Status Updates: As the transportation process progresses, status updates are exchanged between SAP WM and SAP TM. This allows the warehouse to track the shipment's progress and adjust internal processes accordingly.
- Proof of Delivery: Once the goods are delivered and confirmed, SAP TM communicates the proof of delivery (POD) information back to SAP WM, enabling accurate order completion and inventory updates.
Production Integration:
Integration with Production ensures the availability of materials and smooth material flow for production processes. Key integration points include:
Goods Issue for Production: It facilitates the picking and staging of materials required for production orders, ensuring that materials are readily available on the shop floor for the right quantity and the right time.
- Backflushing: After production is complete, inventory levels are updated to reflect the materials used in production, adjusting quantities and locations accordingly.
- Kanban functionality in place as an alternative for staging based on production orders.
- Component Returns: In case of production errors or excess components, returned materials are managed within the warehouse and integrated back into inventory.
- Goods Receipt for Production: (Semi) Finished products are received in the warehouse are made available for the next production step or for sales to the customer.
Material Flow System (API) Integration:
Material Flow Systems manage the automated movement of goods within a warehouse using conveyors, automated storage systems, and other equipment. The Integration involves:
- Task Communication: It communicates tasks (e.g., pick, putaway) to the MFS for execution. The MFS system manages equipment movements to fulfill these tasks.
- Status Updates: The MFS provides real-time status updates on the progress of tasks.
- Error Handling: If there are issues in task execution, such as equipment malfunctions or blockages, the MFS communicates these errors, allowing operators to take corrective actions.
Plant Maintenance Integration:
Integration between SAP WM and Plant Maintenance (PM) ensures that maintenance processes can be performed efficiently while minimizing disruption to warehouse operations. Key integration points include:
- Goods Receipt for Maintenance: When spare parts or maintenance-related materials are received, the integration ensures they are stored correctly and made available for maintenance tasks.
- Goods Issue for Maintenance: Materials required for maintenance activities are picked from the warehouse based on maintenance work orders, supporting timely repairs.
- Reverse Logistics: After maintenance is completed, any unused materials are returned to the warehouse and managed through the inventory processes.
- Coordination: The integration ensures that maintenance schedules align with warehouse availability, preventing conflicts and optimizing equipment uptime.
Cross Topics WM
SAP Fiori Interface:
SAP Fiori is a user experience (UX) design approach that provides a consistent and intuitive user interface across various SAP applications. It provides role-based, responsive, and customizable apps that enable warehouse staff to perform tasks such as order processing, goods receipt, picking, and inventory management. Fiori apps make it easier for users to access relevant information, perform actions, and monitor warehouse operations from various devices.
Best Practices:
SAP S/4HANA Cloud, Public Edition, incorporates best practices derived from industry standards and SAP's expertise. These best practices offer pre-configured and optimized business processes for Warehouse Management. They guide organizations in setting up and using the module efficiently by following proven methodologies. Leveraging best practices can lead to quicker implementation, improved operational efficiency, and adherence to industry standards.
Monitoring & Analytics:
Monitoring and analytics capabilities in SAP S/4HANA Cloud, Public Edition, provide insights into warehouse operations. These capabilities enable users to track key performance indicators (KPIs) and analyze data related to warehouse activities. By visualizing data through dashboards and reports, warehouse managers can identify trends, bottlenecks, and areas for improvement. This information aids in making informed decisions to optimize warehouse processes and enhance overall performance.
In-Apps BAdIs, Custom Fields:
In-Apps BAdIs (Business Add-Ins) and custom fields provide extensibility options within SAP S/4HANA Cloud, Public Edition. These allow organizations to tailor the Warehouse Management module to their specific needs without modifying the standard system. In-Apps BAdIs are predefined enhancement points that enable adding custom logic to standard applications. Custom fields allow adding fields to standard apps to capture additional data. These extensibility features help organizations adapt the system to unique business processes or industry requirements without compromising system upgradability.
Side-by-Side Extensions:
Side-by-Side Extensions refer to the ability to develop and integrate custom applications or features alongside the standard SAP S/4HANA Cloud application. In the context of Warehouse Management, this could involve building specialized tools or functionalities that complement the existing system. For instance, a custom mobile app for warehouse operations can be developed and integrated side-by-side with the standard SAP S/4HANA Cloud interface, offering tailored features for specific user needs.
Synchronous Goods Movements:
Synchronous goods movements refer to real-time updates of inventory movements within the warehouse. In SAP S/4HANA Cloud, Public Edition, goods movements such as goods receipt, goods issue, and stock transfers are updated in real time. This ensures accurate and up-to-date inventory data, enabling warehouse staff and other stakeholders to access reliable information for decision-making.